The automotive industry uses vast amounts of compressed air, which makes timely air leak detection vital for cost and energy efficiency as well as operational continuity.
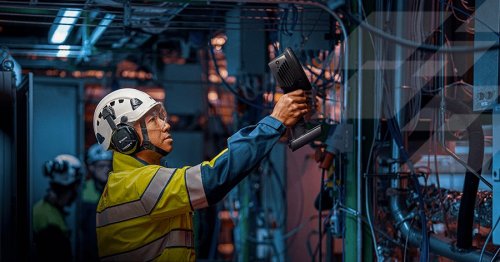
Hidden air leaks are a common nuisance in many industries that rely heavily on compressed air systems. Undetected compressed air leaks can over time lead to severe issues from energy waste and significant financial losses to unplanned outages and even potential safety hazards. Leaks can also contribute to problems with system operations, such as fluctuating system pressure, excess compressor capacity, or decreased service life and increased maintenance of supply equipment. Maintaining compressed air systems by locating and fixing leaks in time is therefore one of the most effective ways of saving energy and improving both productivity and competitiveness.
A challenging environment calls for an advanced solution
The automotive industry is particularly prone to compressed air leaks as vast amounts of compressed air is used both in the production of components and in automotive assembly plants. Also contributing to the high potential for leakages is the large size of the manufacturing facilities, where compressed air is transported in vast pipe networks over long distances. The complex manufacturing lines consist of multiple processes using pneumatic systems with compressed air such as metal casting, metalworking, tool making, CNC machines, assembly robots, sand blasting and car paint booths, all vulnerable to leaks. Common weak points in the equipment include the likes of valves, pipes, hoses, connectors and tools, all found in their hundreds in a single plant. Furthermore, automotive manufacturing facilities are typically noisy environments, which makes locating compressed air leaks extremely challenging.
FLIR Si124 Acoustic Imaging Camera
An acoustic solution that delivers results
Enter the acoustic camera, an advanced predictive maintenance solution that scans large areas and pinpoints the exact location of compressed air leaks quickly and accurately. The camera can be introduced at any stage of the maintenance cycle and the inspections can be carried out without halting operations, using a safe, easily operated device that requires minimal training. In addition to identifying minuscule leaks inaudible to the human ear even in noisy industrial surroundings, the accompanying machine learning-powered analytics software shows leak size and cost estimates and produces actionable data for maintenance and repair plans.
Vast amounts of compressed air is used in automotive assembly plants.
Benefits of an acoustic camera for air leak detection
• Saves time, energy and costs and reduces carbon footprint by locating hidden compressed air leaks in time.
• Ensures operational continuity through early detection of air and gas leaks.
• Scans large areas quickly and pinpoints critical problems accurately, even in noisy industrial environments.
• Requires minimal training and is easy to incorporate into the maintenance cycle.
• Provides real-time results and actionable data for maintenance and repair plans through machine-learning driven analytics.
For more information about thermal imaging cameras or about this application please visit: www.FLIR.com/si124